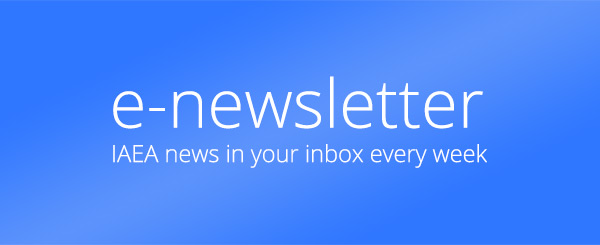
If you would like to learn more about the IAEA’s work, sign up for our weekly updates containing our most important news, multimedia and more.
Next Generation Tools Enable Faster, More Effective Decommissioning of Nuclear Reactors after Severe Accidents
Nayana Jayarajan

Decontamination robot deployed at Fukushima Daiichi to support decommissioning activities
(Photo: The International Research Institute for Nuclear Decommissioning (IRID), Japan)
Within days of the most powerful earthquake ever recorded in Japan, it was apparent that Units 1-4 at the Fukushima Daiichi nuclear power station (NPS) would be shut down permanently. On 11 March 2011, huge tsunami waves caused by the earthquake broke through Japan’s coastal defences, including the perimeter of the NPS, causing extensive damage. Flooding knocked out the emergency generators, causing nuclear fuel in three reactor units to overheat and partially melting the cores. The NPS also experienced several hydrogen explosions which damaged buildings and led to the release of radioactive material. More than 150 000 people were evacuated from the Fukushima prefecture and authorities set up an exclusion zone. However, even once the immediate crisis following the tsunami had largely been resolved, the challenges of decommissioning the heavily damaged facility were just beginning.
Decommissioning a nuclear facility after a severe accident is a complex endeavour and, in comparison with decommissioning after a planned shutdown, often requires specific approaches, techniques and practices. This makes guaranteeing radiation safety while carrying out all operations a major challenge. For instance, one of the most delicate jobs in the decommissioning of a damaged reactor is the removal of spent and damaged fuel.
In the case of the Fukushima Daiichi nuclear accident, some nuclear fuel had melted and fallen to the lower containment sections of reactor units 1, 2 and 3. High levels of radiation inside the containment buildings restricted worker access to the area close to the reactor. The operators faced a major challenge: how were they to remove the damaged fuel when they did not know its exact location?
Enter cosmic-ray muon mapping, a technique that was first deployed over six decades ago and that has been used since in applications from mapping the insides of volcanoes and ancient Egyptian pyramids to detecting nuclear material in shipping containers. Muon tracking devices detect and track naturally occurring, high energy subatomic particles as they pass through materials, using changes in trajectory to determine material density. Nuclear materials such as uranium and plutonium are very dense and, therefore, relatively easy to identify using this technique.
“ Remotely operated robots that carry radiation measurement/visualization tools are a priority area of research and development to help minimize the radiation exposure to site workers, and to systematically advance the decommissioning of Fukushima Daiichi.
Cosmic-ray muon mapping was deployed at the Fukushima Daiichi NPS to estimate the location and condition of fuel debris in the reactor cores. In 2015, experts in Japan developed a modified technique that allowed debris as small as 30 centimetres in size to be tracked. This technique was used to determine the status of the damaged fuel in the Fukushima Daiichi Unit 1 reactor, an essential precursor to decommissioning.
This example is just one of many where technological innovation has been used to solve the unique and unforeseen challenges of post-accident decommissioning and recovery.
“The consequences of an accident are always unpredictable, and existing organizational and technical infrastructure, and available technologies, may not be suitable or sufficient for post-accident needs. Often, when decommissioning damaged nuclear facilities, technological approaches and associated equipment are developed on a case-by-case basis,” said Vladimir Michal, a decommissioning expert at the IAEA, who co-led a project to document and analyse the decommissioning and remediation of damaged nuclear facilities, ‘the International Project on Managing the Decommissioning and Remediation of Damaged Nuclear Facilities’ or DAROD. “In many instances, as in the example of cosmic-ray muon mapping, these technologies found wider application in decommissioning, or even in other industries.”
Another notable example is the construction of a new safe confinement ‘shield’ over the Unit 4 reactor building of the Chornobyl Nuclear Power Plant (NPP) in Ukraine between 2016 and 2019. Constructed to replace the temporary shelter built after the 1986 disaster, it is the largest land-based movable structure in the world and is designed to last a century and to withstand a severe tornado. The new confinement structure was constructed some 180 metres west of the damaged Unit 4. Its construction and subsequent positioning involved the use of state-of-the art civil engineering techniques.
“The new safe confinement does more than prevent the release of radioactive material: it assists with future decommissioning,” said Valeriy Seyda, the Acting General Director of State Specialized Enterprise Chornobyl NPP. The safe confinement structure is designed to prevent the release of radioactive contaminants, protect the internal structures of the reactor and facilitate decommissioning. For the latter purpose, the confinement structure incorporates two state-of-the-art remotely operated cranes. These hang from just under the roof and are designed to allow the eventual decommissioning of Unit 4, while protecting workers and the environment.
At the Fukushima Daiichi NPS, the well-established engineering technique of building a subterranean frozen soil wall was used to prevent groundwater from flowing into the site and mixing with the already-contaminated water inside the reactor buildings. The 1500 metre wall was established by freezing the soil so that it became impermeable to groundwater, thus reducing the overall amount of contaminated water requiring treatment.
Advanced remote operation and robotic technologies can now enable decommissioning work to proceed in areas with high radiation levels. At the Fukushima Daiichi NPS, for example, robots are used for monitoring and measurement, to carry out surveys, for decontamination and to prepare for the removal of fuel debris.
“Remotely operated robots that carry radiation measurement/visualization tools are a priority area of research and development to help minimize the radiation exposure of site workers, and to systematically advance the decommissioning of Fukushima Daiichi,” said Kentaro Funaki, an Executive Director of the Japan Atomic Energy Agency. Funaki highlighted international joint projects as one of the key areas among a wide range of government-funded research and development projects. “Extensive efforts are ongoing to visualize radioactive hotspots in three dimensions near Units 1 and 2 of Fukushima Daiichi. A great deal of success has been achieved by incorporating the results of national and international joint research, and these efforts will continue to be pursued in the future,” he said.
The use of non-nuclear technologies in nuclear environments brings many challenges, including significant development costs, particularly owing to the presence of radiation and uncertainty concerning the precise conditions in which the equipment will operate. However, advances in wiring and other critical components, along with the development of radiation-resistant equipment, make it possible to safely and effectively apply robotic technologies in these challenging environments. In addition, laser technologies enable the interiors in such environments, which are often inaccessible to humans, to be scanned, while protecting the health and safety of workers. “These advances greatly enhance the possibility of safely and effectively dismantling, even in very challenging situations, facilities that have suffered a severe nuclear accident,” said Michal.