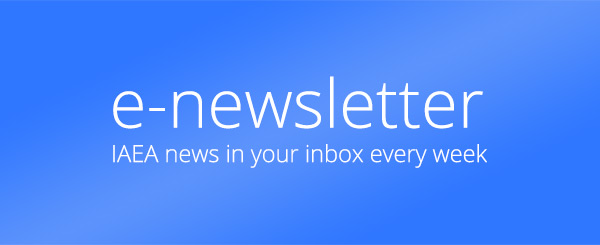
If you would like to learn more about the IAEA’s work, sign up for our weekly updates containing our most important news, multimedia and more.
Leadership and management for safety
Q&A with Operations Director at the Nuclear Research and Consultancy Group (NRG) in the Netherlands
Laura Gil
Safety is paramount in all nuclear installations, research reactors included. Cultivating a culture of understanding among staff of the importance of safety and the measures required to sustain it — a safety culture — is important. A weak safety culture can lead to weak safety measures, which can ultimately affect the well-being of people and the environment. But how do we ensure safety? What are some of the major safety issues in research reactors, and why are leadership and management essential to addressing them? To find out, we interviewed Jelmer Offerein, Operations Director and one of NRG’s five leaders. He has decades of experience in management and leadership for safety.
NRG is a research company of 650 employees that operates the European Commission’s High Flux Reactor, a multipurpose research reactor located in the Netherlands. NRG produces isotopes, conducts nuclear technological research, advises industry on the safety and reliability of nuclear installations and provides services related to radiation protection.
“ If you don’t talk about safety at all, workers don’t know what is expected of them. Leaders need to listen to their staff and know what their concerns are. They also have to motivate and inspire them.
Q: Can you tell us a little about NRG’s strategy and how it approaches safety?
A: NRG’s strategy is quite simple: we want to be the largest medical isotope producer in the world. We started saying in 2008 that we would be a medical isotope producer. Fast forward 11 years and here we are. We are one of the biggest molybdenum-99 producers but still not the largest medical isotope producer. It takes time.
The medical isotope industry is a growing industry. Production volumes increase every year, which is positive, of course, but you have to adapt your organization to that. You need more operators, more equipment, more containers, more tooling, more training and more qualified personnel. And you have to do this in such a way that safety and reliability are not compromised.
To ensure safety, you need a clear strategy. We noticed that, in the past, we were doing a lot of things simultaneously. If people tend to do five or six things at the same time, quality decreases and, if quality decreases, safety levels can also decrease. It’s smarter to do fewer things but do them better. Fewer things but right. And for this, you need a clear focus and strategy in place.
Q: How do leaders and managers influence safety at research reactors?
A: For me, one of the most important things to consider is people’s expectations. We’ve had managers in the past who did not talk about safety at all, and if you don’t talk about safety at all, workers don’t know what is expected of them. Leaders need to listen to their staff and know what their concerns are. They also have to motivate and inspire them.
A leader also has to show exemplary behaviour, particularly when we’re talking about safety. I have a good anecdote to illustrate this. It’s related to how cars are parked at our research reactor facility site — for safety reasons, they must be reversed into a parking spot. One morning, at the beginning of my career, when I had just started working as a managing engineer, I had parked my car in the wrong direction, and one of my co-workers said, “Jelmer, you’ve parked your car the wrong way!” And that’s when I realized that if I park my car the wrong way, everyone would have the right to do it, too. This was a big eye opener; it made me realize the importance of setting an example. In safety, you cannot afford to ‘park your car’ the wrong way. I’ve parked it right ever since.
Q: When talking about safety culture, there is a distinction made between leadership and management. What is this distinction and why is it important to safety?
A: A great illustration of this difference is the fact that managers are behind a group of people telling them what to do and that leaders are part of the group of people, guiding them. For me, managers develop and control the annual plans and make sure they’re implemented. Leaders, in addition, create a vision, tell their people why those plans are necessary and work together with their people on the execution of those plans. Ultimately, a good manager is also a leader and a good leader is also a manager.
Q: What part has the IAEA played in safety at your research reactor?
A: NRG has been working closely with the IAEA for a long time now. The IAEA has helped us by creating a platform to exchange experiences and knowledge and to develop safety guides in close consultation with industry, as well as by visiting us with missions, such as Integrated Safety Assessment of Research Reactors (INSARR) missions, that were heavily focused on safety in a technical way. Since we also wanted to know the status of our safety culture and receive input on which areas to improve, we requested an IAEA Independent Safety Culture Assessment (ISCA) mission.
In 2017, an expert-led ISCA team came to assess our safety culture. They reviewed documents, interviewed workers, looked into our integrated management system, as well as our training and qualification programme, and organized focus groups to see the dynamics and interactions between employees. The ISCA report showed we were definitely on the right track, but there were areas for improvement.
One of these was our island culture; we have different installations with large security fences around them, which makes it hard for employees to meet. For security reasons, that’s perfect, but if you want to closely interact with colleagues on all kinds of topics, it is not ideal. We also worked on improving the descriptions of our roles and responsibilities and the integration of those roles into our management system.
We worked on these areas. The team came back 18 months later to look at the implementation of the recommendations and found that we had made progress in improving our safety culture. Of course, we are never quite finished — the world around us is changing quite rapidly, so we always have to keep improving and adapting.